Challenges and Solutions in Web Guiding for Wide-Format Printing
Accurate web guiding is critical in wide-format printing to enable precise substrate alignment and registration, maximizing print quality while minimizing waste. However, achieving precise web guiding in wide-format printing presents unique challenges. This article explores the key challenges faced in web guiding for wide-format printing and presents innovative solutions to overcome them, ensuring optimal performance and efficiency in the printing process.
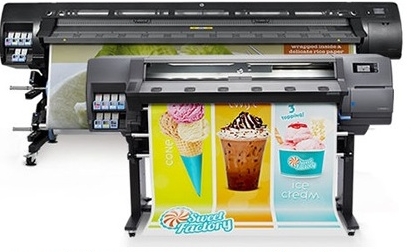
Basics of Web Guiding
Concept | Description |
1. Web Guiding | Web guiding is a process used in various industries to ensure the alignment and positioning of a moving web of material as it passes through processing machinery. |
2. Types of Web Guiding Systems | Passive Web Guiding: Relies on external forces such as tension, gravity, or friction to align the web. Active Web Guiding: Utilizes sensors and actuators to detect and adjust the position of the web in real time. |
3. Components of Web Guiding Systems | Sensor: Detects the lateral position of the web and sends signals to the control system. Actuator: Receives signals from the control system and adjusts the guiding mechanism to correct the web position. Control System: Processes sensor signals and sends commands to the actuator for web alignment. |
4. Operating Principle | Feedback Loop: The sensor continuously monitors the web position and provides feedback to the control system. Control Algorithm: The control system calculates the necessary adjustments based on the deviation from the desired position and sends commands to the actuator to correct the web alignment. |
5. Applications | Web guiding systems are used in various industries such as printing, packaging, papermaking, and converting to ensure precise alignment of webs during processing. |
6. Benefits | Improved Product Quality: Ensures consistent alignment of webs, reducing defects and waste. Increased Efficiency: Minimizes downtime caused by web misalignment, leading to higher productivity. Reduced Material Waste: Prevents material wastage due to misalignment, resulting in cost savings. |
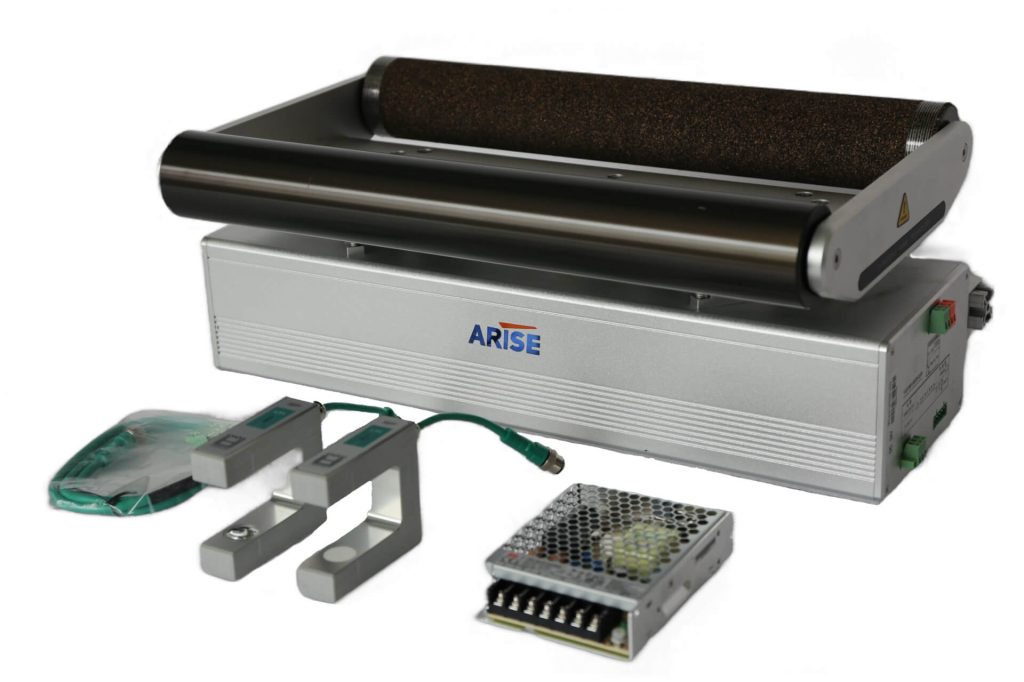
Challenges in Web Guiding for Wide-Format Printing
1. Substrate Variability
Wide-format printing frequently employs a variety of substrates, including vinyl, cloth, paper, and rigid materials. Each substrate type has different thickness, surface texture, and elasticity, making it difficult to maintain constant web tension and alignment during printing.
2. Dynamic Environmental Conditions
Wide-format printing settings are subject to temperature, humidity, and airflow changes, which can affect the dimensional stability of the printing substrate. These variances affect web tension and alignment, resulting in misregistration and print flaws.
3. Web Flutter and Vibration
High-speed printing and substrate movement can induce web flutter and vibration, especially with lightweight or flexible materials. This dynamic behavior makes it difficult to achieve precise web guiding, resulting in inaccurate registration and print quality issues.
4. Edge Detection and Tracking
Accurate edge detection and tracking are essential for effective web guiding. However, challenges such as substrate transparency, irregular edges, and poor contrast make it difficult for sensors to detect and track the substrate edges reliably.
5. Integration with Printing Equipment
Integrating web guiding systems with wide-format printing equipment, such as digital printers, laminators, and cutters, requires seamless communication and synchronization. Incompatibilities or communication delays between systems can disrupt the printing process and compromise productivity.
6. Maintenance and Calibration
Regular maintenance and calibration of web guiding systems are required to ensure optimal performance and accuracy. However, scheduling and carrying out maintenance operations presents complications, potentially resulting in downtime and production interruptions.
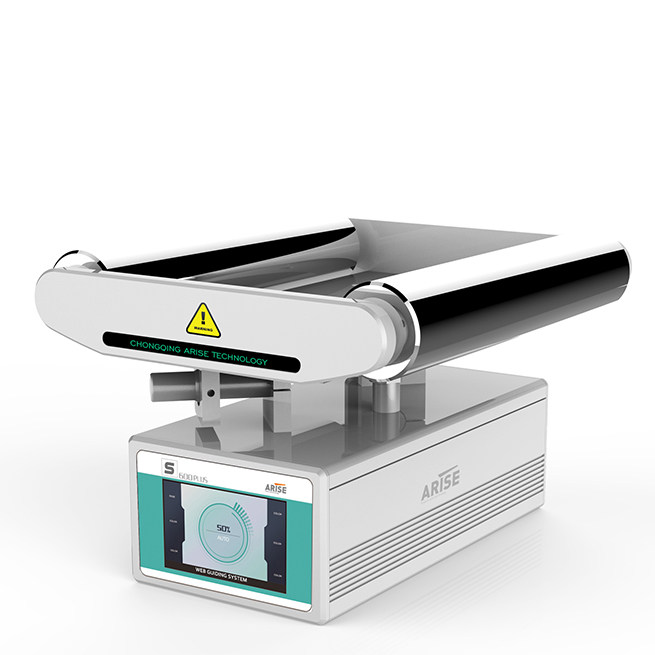
Solutions to Overcome Challenges in Web Guiding for Wide-Format Printing
1. Advanced Sensor Technologies
Using advanced sensor technologies, such as laser sensors and vision systems, improves edge detection and tracking accuracy. These sensors give real-time feedback on substrate position, allowing for precise modifications to the web guiding system to keep the substrate aligned despite variations.
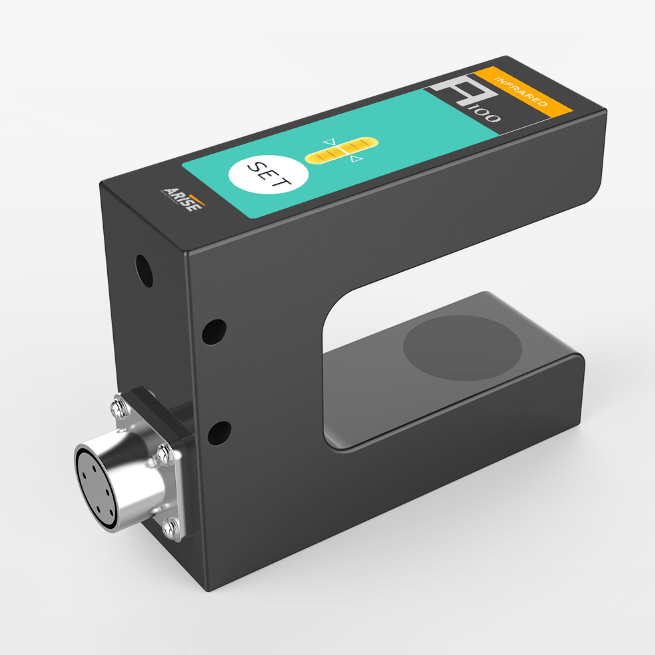
2. Active Web Tension Control
Implementing active web tension control mechanisms, such as pneumatic brakes or servo-driven unwind/rewind systems, provide a proactive option for reducing web flutter and vibration. These systems enable stable web movement and reliable guidance by dynamically altering tension levels in response to substrate conditions.
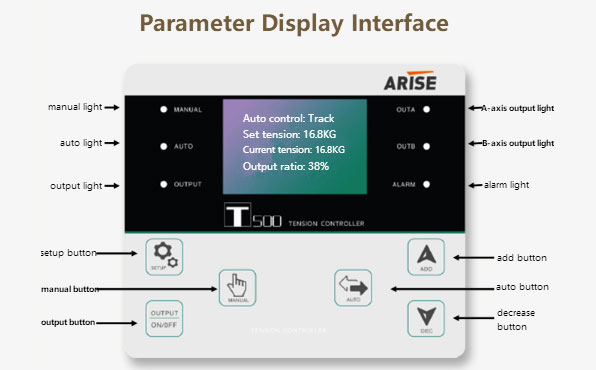
3. Dynamic Web Guiding Algorithms
Developing intelligent web directing algorithms that can adjust to changing environmental conditions and substrate activity is critical. These algorithms use predictive modeling and feedback systems to continually refine guiding parameters, which improves accuracy and responsiveness.
4. Mechanical Stabilization Techniques
Employing mechanical stabilization techniques, such as tension rollers and web spreaders, provides a physical solution to mitigate web flutter and vibration. These devices maintain consistent substrate tension and alignment, minimizing deviations during the printing process.
5. Integration and Automation
Enhancing integration and automation between web guiding systems and printing equipment streamlines operations and reduces human error. By utilizing standardized communication protocols and seamless interfacing, printers can achieve synchronized control and improved efficiency.
6. Environmental Control Measures
Implementing environmental control measures, such as climate-controlled printing environments and dust extraction systems, helps stabilize substrate conditions. By minimizing temperature fluctuations, humidity levels, and airborne contaminants, printers can maintain consistent substrate behavior and improve guiding accuracy.
7. Regular Maintenance and Calibration
Instituting a proactive maintenance program and calibration procedure ensures that web guiding systems work well over time. Printers can minimize downtime and improve guiding accuracy by performing frequent inspections, cleaning, and adjustments.
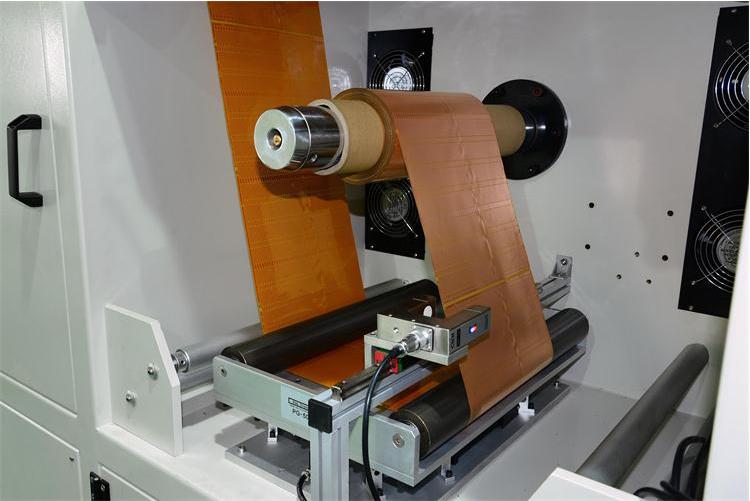
Conclusion
Web guiding is a critical aspect of wide-format printing because it ensures accurate alignment and registration of printing substrates, resulting in optimal print quality and productivity. Printers may improve the performance, efficiency, and reliability of web guiding systems by addressing these challenges and applying efficient solutions, hence opening up new prospects for innovation and growth in wide-format printing.