Automatic vs. Manual Web Guiding: Which is Better for Your Application
In web handling systems which are used in industries such as printing, packaging, textiles, and paper converting, maintaining accurate alignment of the moving web is critical. Web guiding systems are employed to ensure that materials are processed efficiently and accurately without deviation. These systems come in two main types: manual web guiding and automatic web guiding. Choosing the right web guide system depends on factors such as production scale, precision requirements, budget, etc.
Table of Contents
Understanding Web Guiding
Web guiding refers to the method of controlling the lateral position of a continuous web of material as it moves through a production process. Any misalignment can result in material waste, poor product quality, or even equipment damage. The goal is to maintain the web’s position within a specified tolerance throughout the process.
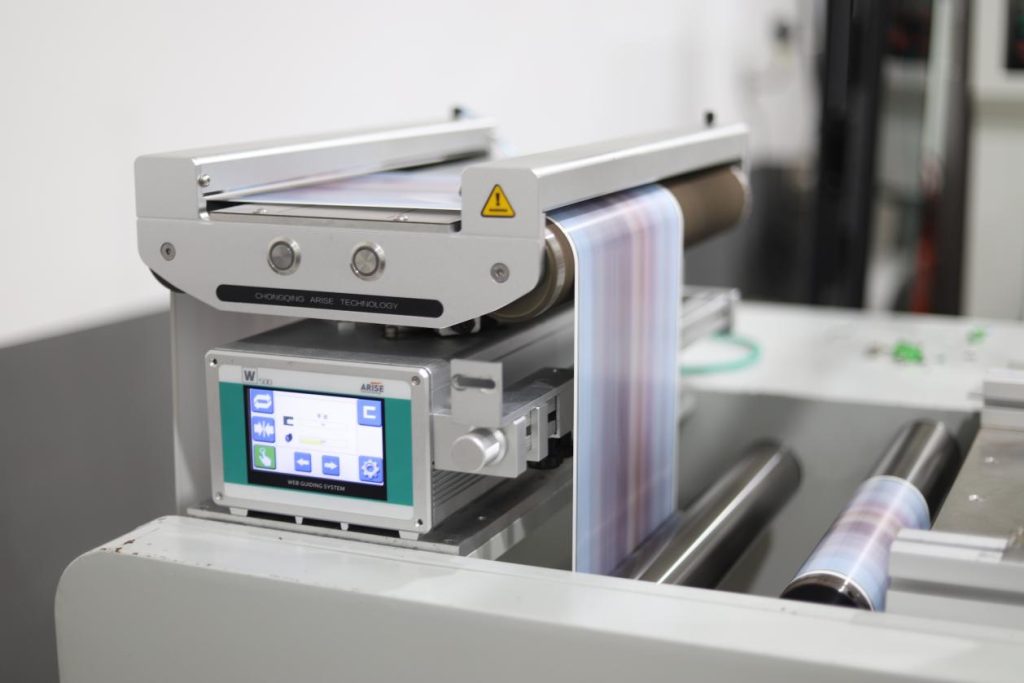
Understanding Automatic Web Guiding Systems
An automatic web guiding system monitors the position of a moving web and makes real-time corrections to keep it aligned within preset tolerances. It uses sensors to detect the edge or center of the web, a controller to process the data, and actuators (usually stepper motors or pneumatic devices) to adjust the guide rollers or the web’s path accordingly.
These web guide control systems are particularly suited for high-speed or high-precision operations, where manual adjustments would be too slow or inaccurate. Automatic web guiding improves product quality, reduces labor requirements, and supports continuous or unattended operation.

Main Components
- Web Guide Sensors: Detect the position of the web edge or center using ultrasonic, infrared, or optical technology.
- Web Guide Controller: Receives signals from the sensors and determines the necessary corrective action.
- Web Guide Actuators: Mechanically adjust the roller or web path to correct misalignment. These are usually electric motors or pneumatic cylinders.
- Web Guide Mechanism: Includes pivoting or shifting rollers that respond to actuator movements to realign the web.
- Human-Machine Interface (HMI): Optional user panels for setup, calibration, and system monitoring.
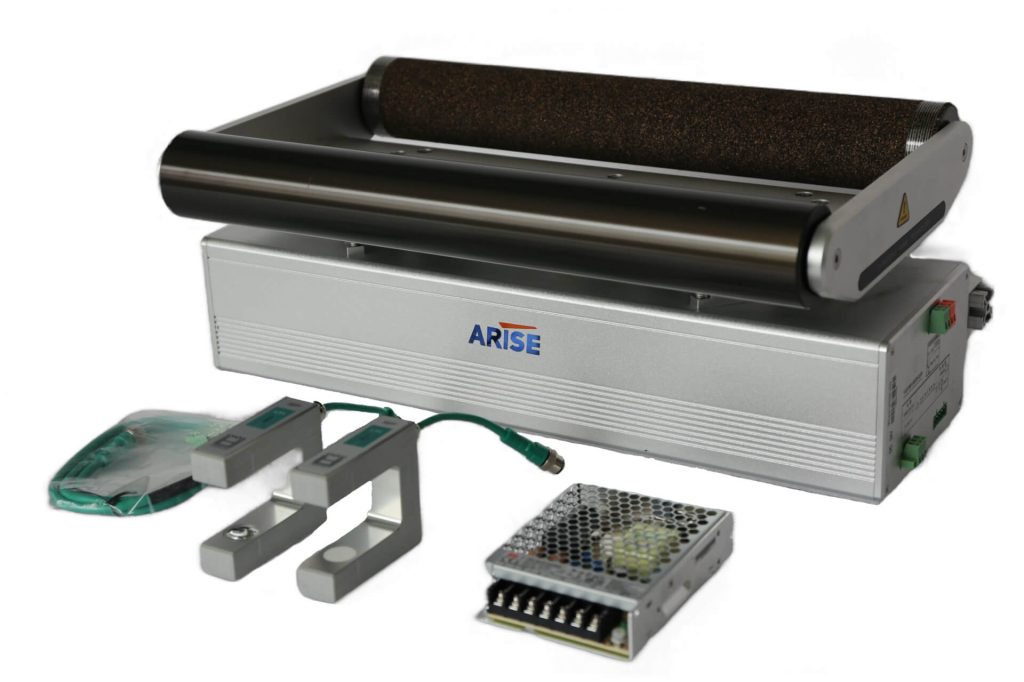
Advantages
- High Accuracy: Maintains web alignment within very tight tolerances, even at high speeds.
- Labor Savings: Eliminates the need for constant human monitoring and manual corrections.
- Increased Efficiency: Reduces downtime and scrap, improving overall production throughput.
- Real-Time Correction: Makes instant adjustments, which is critical in processes like printing or laminating.
- Consistency: Delivers repeatable performance across shifts, operators, and product runs.
Limitations
- Higher Initial Cost: Requires investment in sensors, controllers, and actuators.
- Complexity: Installation and troubleshooting may require trained personnel.
- Maintenance Needs: Electronic components and motors may need periodic calibration or servicing.
Applications
- Printing presses (for maintaining print registration)
- Packaging machinery (for sealing and folding precision)
- Textile and nonwoven processing
- Film and foil production
- Lamination and coating lines
- Battery and electronics manufacturing
Understanding Manual Web Guiding Systems
A manual web guiding system is a mechanical setup that allows operators to adjust the alignment of a moving web using hand-operated tools. These systems typically do not include motors, sensors, or electronic controllers. Instead, the operator monitors the web visually or through passive indicators and makes real-time adjustments using knobs, levers, or guiding rollers.
This type of web guide system is particularly useful for slower production lines or processes where alignment changes are infrequent. It gives operators complete control over web positioning, which can be advantageous in environments where flexibility and direct interaction are required.
Key Components
- Steering Rollers: These are rollers that the operator can adjust laterally to influence the web’s path.
- Adjustment Mechanism: Handwheels or levers are used to shift guide rollers or the web path based on visual feedback.
- Guide Frames: Mechanical frames that support the web path and guide components.
- Edge Indicators: Visual marks or mechanical guides that help the operator judge whether the web is tracking correctly.
- Operator Interface: The human element, involving constant monitoring and physical adjustments to maintain alignment.
Advantages
- Cost-Effective: Manual systems are significantly cheaper than automatic setups, both in terms of initial investment and maintenance.
- Simplicity: With no electronics or software, manual systems are easy to understand, operate, and repair.
- Flexibility: Ideal for short production runs, product testing, or applications where web characteristics frequently change.
- Operator Control: Allows skilled workers to fine-tune the web alignment based on visual cues and personal experience.
Limitations
- Operator Dependency: System performance relies heavily on the attention and skill of the operator.
- Lower Precision: Manual web guide systems may not achieve the tight tolerances required in high-end production environments.
- Unsuitable for High-Speed Lines: At higher speeds, the need for rapid corrections makes manual adjustment impractical.
- Inconsistency: Varying skill levels and shifts may lead to inconsistent product quality.
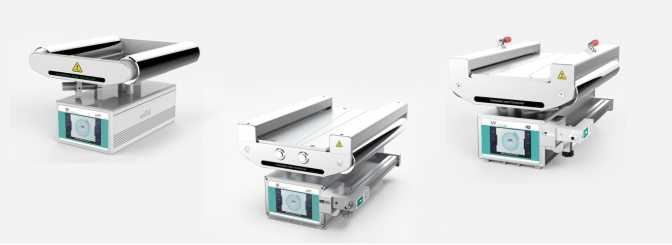
Key Differences Between Automatic vs. Manual Web Guiding
Aspect | Automatic Web Guiding | Manual Web Guiding |
Operation | Sensor-based, real-time correction | Hand-operated, visual correction by operator |
Precision | High accuracy with tight alignment tolerances | Lower precision, depends on operator skill |
Speed Compatibility | Suitable for high-speed production lines | Best for low to moderate speed processes |
Labor Requirement | Minimal, requires little to no manual intervention | High, requires continuous monitoring and adjustment |
Initial Investment | Higher due to sensors, actuators, and controllers | Lower, with basic mechanical setup |
Maintenance | Requires occasional calibration and servicing | Minimal, mostly mechanical upkeep |
Consistency | Uniform performance regardless of shift/operator | May vary depending on operator attention and experience |
Setup Complexity | Requires technical expertise for installation | Simple to install and operate |
Adjustment Response Time | Instantaneous and automatic | Delayed and dependent on human response |
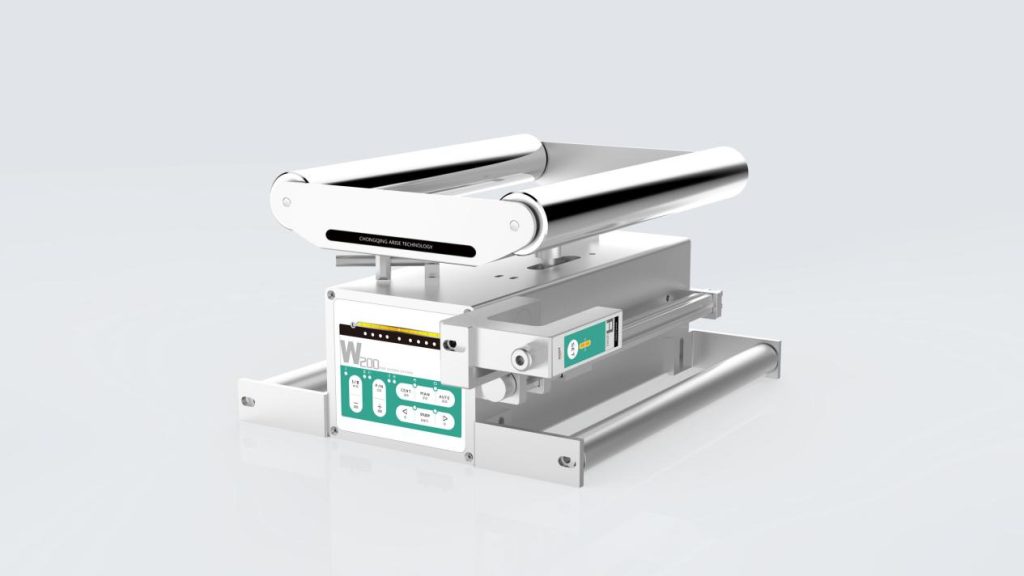
Choosing the Right System Between Automatic vs. Manual Web Guiding
1. Understanding the Operational Environment
The first step in deciding between an automatic and manual web guiding system is assessing the operational conditions. In high-speed or high-volume environments, even a minor deviation in web alignment can result in substantial material waste or machine downtime. In contrast, slower operations with occasional adjustments may not justify the cost of automation.
2. Evaluating Application Requirements
Several application-specific requirements influence the selection:
Requirement | Automatic Web Guiding | Manual Web Guiding |
Production Speed | Ideal for high-speed lines | Suitable for low to moderate speeds |
Precision/Tolerance Control | Needed when tight tolerances or alignment are critical | Acceptable when minor deviations are tolerable |
Operator Involvement | Minimal, automated corrections | High, continuous visual checks and manual adjustments required |
Labor Availability | Best where skilled labor is limited or costly | Works well where skilled operators are readily available |
Budget Constraints | Higher upfront cost, long-term savings | Lower initial cost, manual effort increases over time |
Production Volume | Suitable for high-volume, continuous operations | Best for low-volume, short-run applications |
Changeover Frequency | Handles frequent roll/web changes efficiently | Less suited for frequent changeovers |
Complexity of Web Path | Adapts easily to complex or multi-stage web paths | Better for simple, straight-through web paths |
Consistency Requirements | Delivers repeatable, uniform performance | Performance may vary with operator or shift |
3. Considering Long-Term Efficiency
Beyond the initial setup, long-term productivity should also be part of the equation. Automatic systems contribute to operational stability and quality control, especially when frequent roll changes or web width variations are involved. They allow for real-time corrections that manual systems simply can’t match, which becomes crucial when scalability is part of the production strategy.
Summary
Selecting between automatic and manual web guiding systems involves balancing cost, control, and production demands:
- Choose automatic web guiding if your operation demands precision, consistency, and high throughput.
- Choose manual web guiding if your process is simple, budget-conscious, and run by experienced operators in low-speed environments.
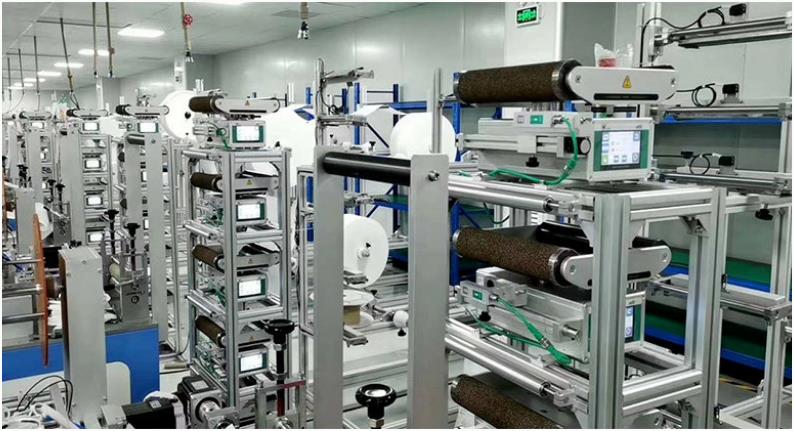
Final Thoughts
The decision between automatic vs. manual web guiding hinges on your specific operational needs. For modern manufacturing processes aiming for greater productivity and minimal waste, the automatic web guide system is increasingly becoming the standard.