Advancements in In-line Width/Thickness Measurement Systems
In-line width and thickness measurement systems are integral to modern manufacturing processes, ensuring products meet stringent quality standards and specifications. As industries demand higher precision and accuracy, advancements in measurement technologies have become essential. This article explores the latest enhancements in in-line width/thickness measurement systems that improve precision and accuracy, contributing to more efficient and reliable manufacturing operations.
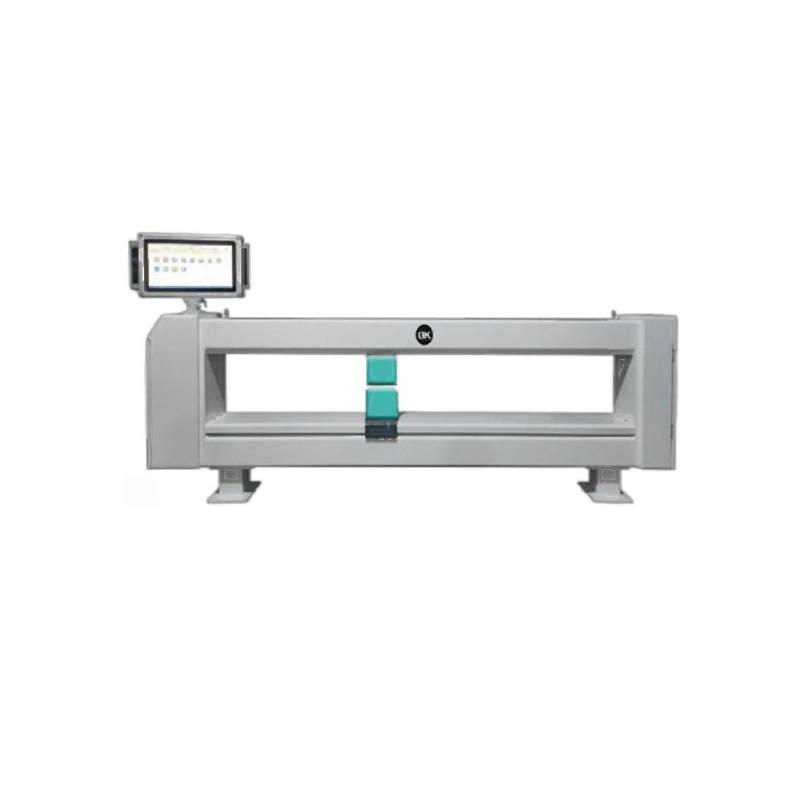
Advanced Sensor Technologies for In-line Width/Thickness Measurement Systems
1. Laser-Based Sensors
- Laser sensors offer high precision and rapid response times, making them ideal for in-line measurement. Technologies such as laser triangulation and time-of-flight are increasingly used to measure dimensions with sub-micron accuracy.
- Laser Triangulation: This method involves projecting a laser beam onto the surface of the material and measuring the reflected light’s angle. The system then calculates the distance and thickness based on the triangulated angle.
- Time-of-Flight (ToF): ToF sensors measure the time taken for a laser pulse to travel to the target and back. This technology provides high precision and is suitable for a variety of materials and surfaces.
2. Capacitive Sensors
- Capacitive sensors measure changes in capacitance caused by the distance between the sensor and the material. They are particularly useful for non-contact measurement of conductive and non-conductive materials.
- These advanced sensor technologies offer high resolution and are capable of detecting minute changes in thickness, making them suitable for applications requiring high precision.
3. Ultrasonic Sensors
Ultrasonic sensors use high-frequency sound waves to measure thickness. They are particularly effective for materials where optical methods may not work, such as opaque or textured surfaces. These sensors provide reliable, non-destructive measurements with high precision.
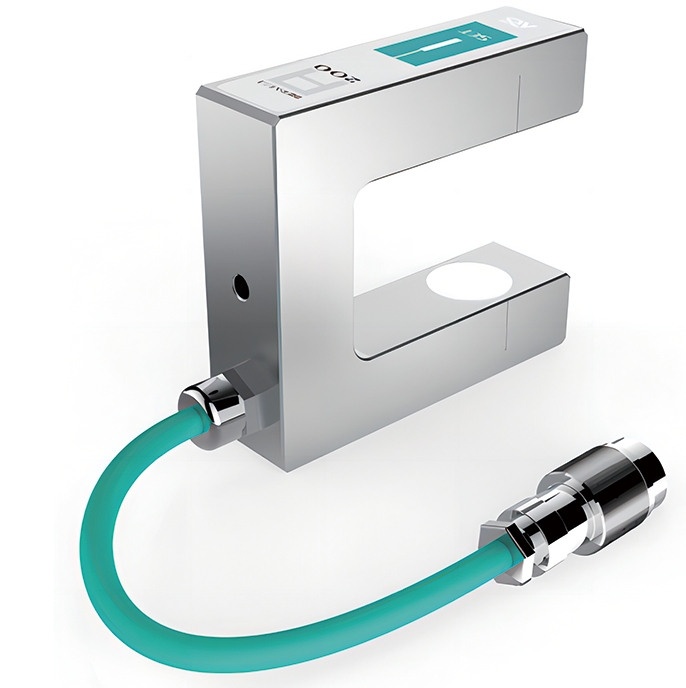
Integration of Machine Learning and AI in In-line Width/Thickness Measurement Systems
Predictive Analytics
- Machine learning algorithms analyze data from measurement systems to predict potential deviations in real-time. This allows for immediate adjustments in the manufacturing process, ensuring consistent product quality.
- AI-driven analytics can identify patterns and anomalies that human operators might miss, enhancing the overall accuracy of the measurement system.
Adaptive Algorithms
AI algorithms continuously learn from the measurement data, improving their accuracy over time. These adaptive systems can adjust to changes in material properties, environmental conditions, and other variables, maintaining high precision in diverse manufacturing environments.
Enhanced Calibration Techniques for In-line Width/Thickness Measurement Systems
1. Automated Calibration
Routine Automated Calibration
- Automated calibration systems perform routine checks and adjustments without manual intervention. These systems can be programmed to calibrate at specific intervals or in response to certain triggers, ensuring consistent accuracy over time.
- Automated routines reduce human error, minimize downtime, and ensure that the system is always operating at peak performance.
Real-time Calibration
- Real-time calibration adjusts the measurement system continuously during operation. Sensors detect changes in environmental conditions or material properties, and the system automatically recalibrates to maintain accuracy.
- This approach is particularly useful in high-speed production environments where manual calibration would be impractical.
2. Environmental Compensation
Temperature Compensation
- Temperature fluctuations can affect measurement accuracy. Advanced systems incorporate temperature sensors to monitor the environment continuously. Calibration algorithms adjust measurements based on these temperature readings to ensure consistent accuracy.
- Some systems use materials with low thermal expansion for critical components to reduce the impact of temperature changes.
Humidity and Vibration Compensation
- Humidity and vibration can also impact measurement precision. Enhanced calibration techniques include sensors that monitor these factors and algorithms that adjust measurements accordingly.
- Vibration isolation mechanisms can be employed to physically reduce the impact of vibrations on the measurement system.
3. Advanced Reference Standards
High-Precision Reference Standards
- Using high-precision reference standards for calibration ensures that the measurement system can be accurately compared and adjusted. These standards are often traceable to national or international measurement standards, providing a benchmark for calibration.
- Reference materials with well-known properties are used to calibrate the system, ensuring it meets the required accuracy specifications.
Dynamic Reference Standards
- Dynamic reference standards that simulate actual production conditions can be used to calibrate the system under realistic scenarios. This approach helps ensure that the system performs accurately under typical operating conditions.
- These standards can include moving materials or varying thicknesses and widths to better reflect real-world variations.
4. Remote and Cloud-Based Calibration
Remote Calibration
- Remote calibration allows experts to calibrate measurement systems from off-site locations. This capability is particularly useful for systems in remote or hazardous environments where on-site calibration would be difficult.
- Remote diagnostics can also identify calibration needs and issues before they impact production.
Cloud-Based Calibration Management
- Cloud-based systems can store calibration data and algorithms, providing a centralized platform for managing calibration across multiple systems and sites. This ensures consistency and allows for easier updates and improvements.
- Data analytics in the cloud can provide insights into calibration performance and identify trends that could indicate the need for adjustments.
High-Resolution Imaging Systems in In-line Width/Thickness Measurement Systems
Optical Coherence Tomography (OCT)
OCT uses light waves to capture high-resolution, cross-sectional images of materials. This technology is particularly useful for measuring the thickness of layered materials and coatings, providing detailed insights without damaging the material.
High-Speed Cameras
High-speed cameras capture detailed images of the material as it moves through the production line. Combined with advanced image processing algorithms, these cameras can measure width and thickness with high precision and at high speeds, enabling real-time quality control.
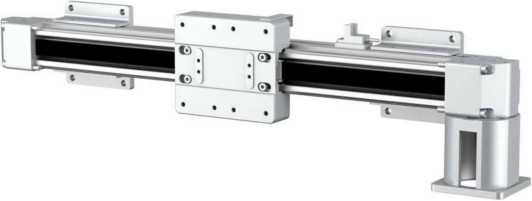
Integration with Manufacturing Execution Systems (MES) in In-line Width/Thickness Measurement System
Real-Time Data Integration
Integrating measurement systems with MES allows for seamless data flow between the measurement instruments and production control systems. This real-time data integration enables immediate process adjustments, ensuring products remain within specified tolerances.
Closed-Loop Feedback
Closed-loop feedback systems use measurement data to automatically adjust production parameters. By continuously monitoring and fine-tuning the manufacturing process, these systems maintain high precision and accuracy, reducing waste and improving product quality.
Hybrid Measurement Systems in In-line Width/Thickness Measurement System
Combination Technologies
Hybrid measurement systems that integrate multiple measurement technologies (e.g., laser and capacitive) offer the advantages of each method. This combination enhances measurement accuracy and versatility, making these systems suitable for a broader range of applications and materials.
Multi-Sensor Fusion
Multi-sensor fusion combines data from different types of sensors to provide a comprehensive and accurate measurement profile. This approach improves measurement reliability and compensates for the limitations of individual sensor technologies.
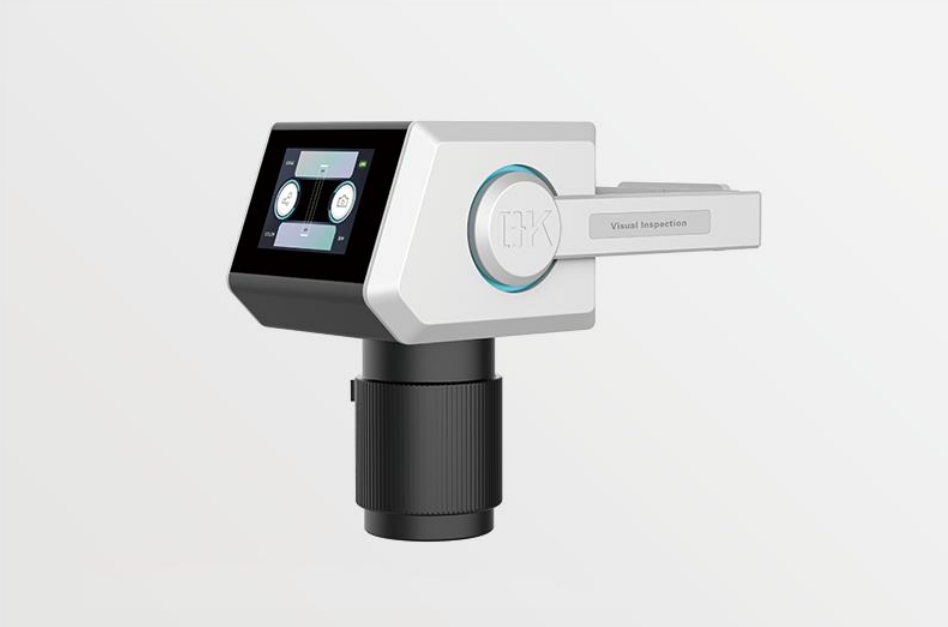
Conclusion
Advancements in in-line width and thickness measurement systems are significantly enhancing precision and accuracy in manufacturing. These advancements not only ensure consistent product quality but also streamline manufacturing processes, reduce waste, and lower operational costs.