About Web Guiding System, What You Need To Know
Rupture and breakage of web material caused by the use of mechanical baffle rectification occur frequently in the production of traditional production lines, resulting in material and time loss. Furthermore, if the material web changes during production, the misalignment will result in waste material remaining on the machine, and the operator will need to clean the residual paste to continue production, reducing the efficiency of the production line. The web guiding system can achieve multi-layer material alignment, doubling the speed, eliminating waste, and preventing machine sticking.
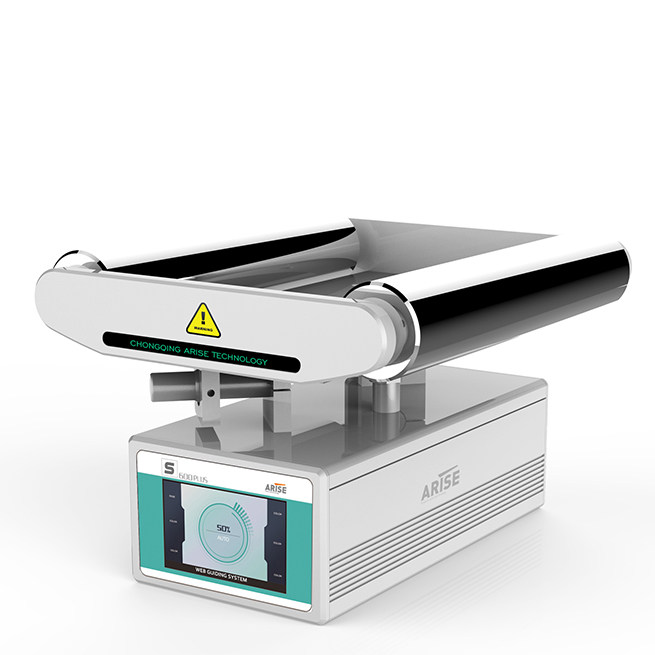
Three Types Of Web Guiding System
Unwinding web guiding
It ensures that the coiled material is always exported from the preset position during the unwinding process, so as to accurately enter the next process.
Precautions for design and installation
the unwinding movable rack and the guide roller are integrated. When the driver performs telescopic action, the unwinding movable rack and the guide roller act together. The edge detection sensor should be installed behind the guide roller and fixed independently. If it is a photoelectric sensor, it should be irradiated on the movable guide roller or other guide rollers integrated with the roll rack, that is, when the driver acts, The guide roller irradiated by the photoelectric sensor also moves along with the unwinding movable frame following the driver.
Ongoing web guiding
This process ensures that the coiled material always passes through the preset position during the process of moving, to prevent uneven edges when materials entering the next process.
Precautions for design and installation
The edge detection sensor needs to be fixed independently. If it is a photoelectric sensor, it needs to be illuminated on the nearest fixed guide roller or fixed baffle after the web guiding frame export roller.
Winding web guiding
It ensures that the winding edge is neat during winding.
Precautions for design and installation
Winding web guiding is very similar to unwinding web guiding, but installation is quite different. The web guide sensor is integrated with the winding movable frame, and the driver performs telescopic action. The web guide sensor and the winding movable frame move together and the guide roller is fixed independently after the edge detection sensor. If it is a photoelectric sensor, it should be irradiated on the independently fixed inverted roller.
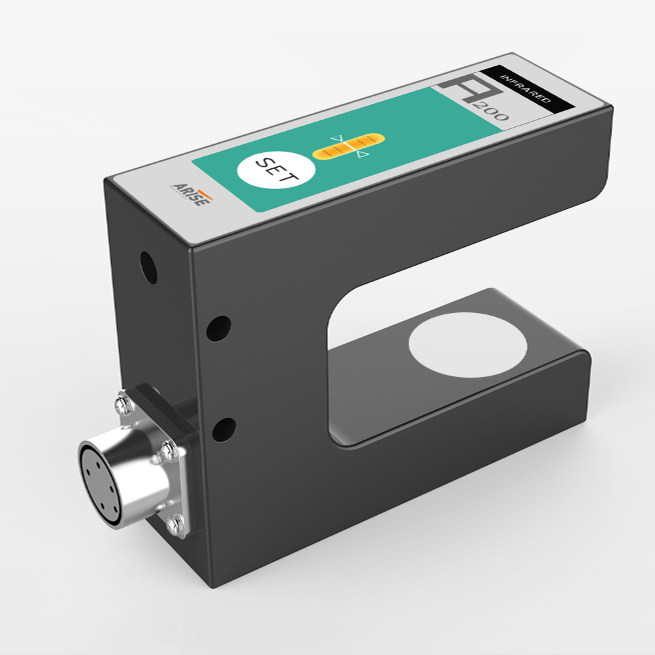
Different Applications Of Web Guiding System
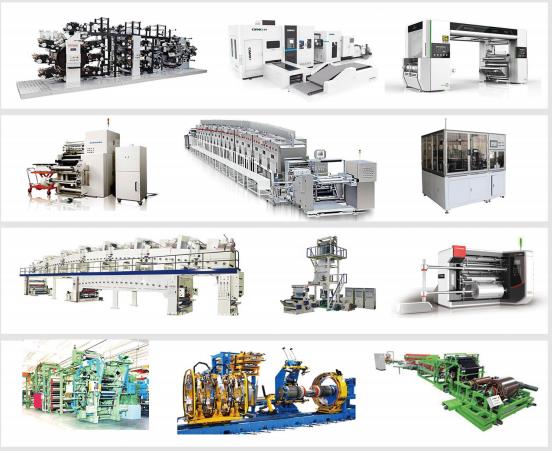
Web guiding system has a wide range of applications and is applicable to a variety of different materials. The Arise all-in-one web guide machine can guide the position of paper, corrugated paper, plastic film, woven material, glass fiber, printed pattern, textile fiber, textile material with lines, holographic pattern, aluminum foil and copper foil, etc. The sensor accuracy can reach 0.01mm and the waterproof and dust-proof sensor can be customized.
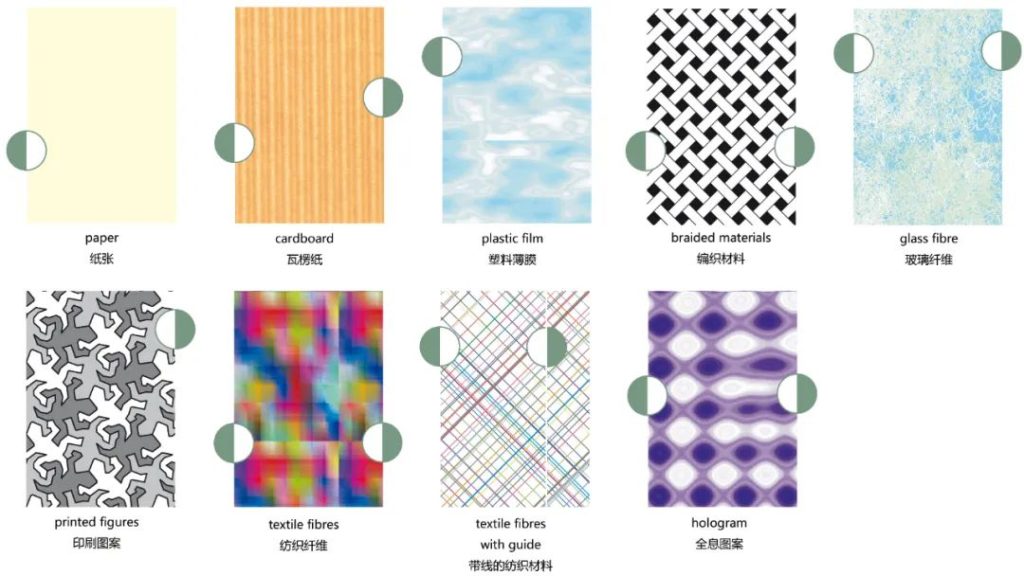
When used for winding and unwinding, Arise web guide equipment provides the drivers of various thrust and stroke to meet the thrust requirements of different materials.
When used in a process of ongoing, Arise can customize the web guide system of different sizes for customers.
Arise also specially designed a composite web guide system for the composite machine. The main sensor installed on the automatic bracket is used to detect the position of the web material, and the secondary sensor is often used to detect the position of the composite material.
Summary
The Arise web guiding system has wide applications. It is distinguished by its quick response time, high accuracy, and high stability. It is critical in the production of web materials such as packaging, printing, non-woven fabric, corrugated paper processing, and so on.