A Few Tips To Know Tension Control
In the process of winding or unwinding, the quality and efficiency of production should be guaranteed. Tension control is very important. If the tension is too small, the coil is easy to loosen and causes lateral drift. If the tension is too large, the surface of the coiled material will wrinkle or even break.
Functions Of Tension Control
The tension controller directly affects the product quality. The tension control system is one of the core elements of the printing machine. Its performance reflects the performance of the gravure press. The tension control system plays the following roles
1. According to the change law of tension, control the uncoiling speed of coil.
2. According to the direction of overprinting error, change the local tension in printing to achieve higher overprinting accuracy.
3. Adjust the speed of the winding shaft to make the winding neat.
4. Eliminate the tension fluctuation caused by the film itself.
5. Control and adjust the motion speed of the film.
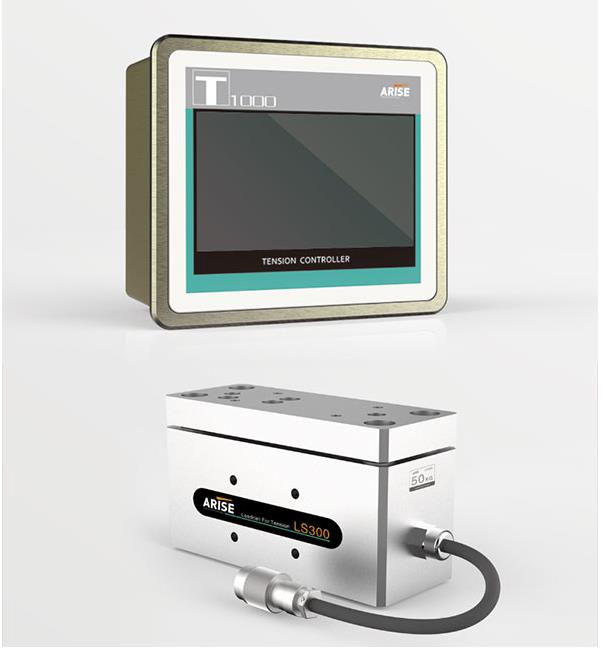
Factors Affecting Tension Control
During the printing process, the tension of the film roll is constantly changing during the movement, which is mainly caused by the following factors
1. In the process of winding and unwinding, the diameter of the unwinding and rewinding is variable, and the change of the diameter will cause the change of the coil tension.
2. The shape of the membrane roll is not a standard cylinder, with a certain degree of eccentricity and local deformation. The weight of the coil is inconsistent.
3. The thickness of the film is uneven.
4. There are pressure differences and diameter differences between each roller, and the tension between each printing unit is inconsistent.
5. When the operating state of the printing machine changes, such as the increasing speed, decelerating speed, start, brake, and roll change, the tension changes greatly.
6. The change of the lifting speed of the machine will inevitably cause the change of the tension of the whole machine.
7. In the process of rewinding and unwinding, the diameter of winding and unwinding is constantly changing, and the change of diameter will inevitably cause the change of raw material tension. Under the condition that the braking torque of unwinding is constant, the diameter decreases and the tension increases. On the contrary, if the winding torque is constant, the tension will decrease as the winding diameter increases.
8. The change of the tightness of the raw material roll will also affect tension control of the whole machine.
9. Non-uniformity of printing raw materials
For example, the fluctuation of material elasticity, the change of material thickness along the width and length direction, the mass eccentricity of the coil, and the change of production environment temperature and humidity will also affect the tension control of the whole machine
10. The change of speed during printing affects the tension control. When the running speed is increased or decreased, the main motor speed changes. First of all, it causes the instantaneous change of the tension of the material from the unwinding traction to the rewinding section, and the tension must be stabilized gradually after a period of small vibration of the material.
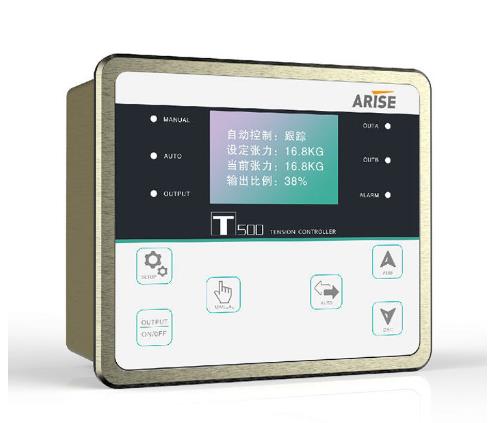
The methods of tension control
The tension control methods are generally divided into manual control and automatic control, and automatic control can be divided into constant tension control and taper tension control.
In terms of automatic tension controller, it includes open-loop semi-automatic tension controller and closed-loop full-automatic tension controller. The open-loop semi-automatic tension controller adjusts the coil tension by detecting the change of coil diameter, that is, taper tension control.
The full-automatic tension controller directly detects the tension of the coil through the tension sensor or tension detector and feeds back to the controller. The controller adjusts the output according to the detection signal to ensure the constant tension of the coil.