A Few Quick Tips to Operate and Test The All-in-one Web Guide System
Arise all-in-one web guiding system can achieve multi-layer material alignment and there is no waste in the refueling process. The web guide system is an edge position controller for tracking the edge of the coil materials or printing lines for high-accuracy differential and swing. It is composed of large-scale industrial integrated circuits and has the advantages of high reliability and long service life.
Now we introduce a few tips to operate and test the guiding system after installation
Operation of the main interface
1. Install the rack and the all-in-one machine, plug the power and sensor plugs of the all-in-one into the corresponding sockets, and power on.
2. Enters the “manual” mode of the main interface and touches the “function menu” button. Then touch the “self-learning” button to enter the all-in-one self-adaptation and automatically return to “manual” mode.
3. Touch the “back to center” button, and then touch the “manual” button, respectively pressing the material of the same layer into the material according to the “material penetration diagram”. Run the main machine for a few minutes to move the material for a period of time.
4. In the “manual” mode, adjust the sensor’s position and the moving bracket in a large range and then adjust the rotary knob in a small range. (Adjust the position to the sensor offset display about 50%)
5. In the “automatic” mode, adjust the edges of the other layers of materials to coincide with the edges of the reference based on one layer, and the correction and debugging are completed.
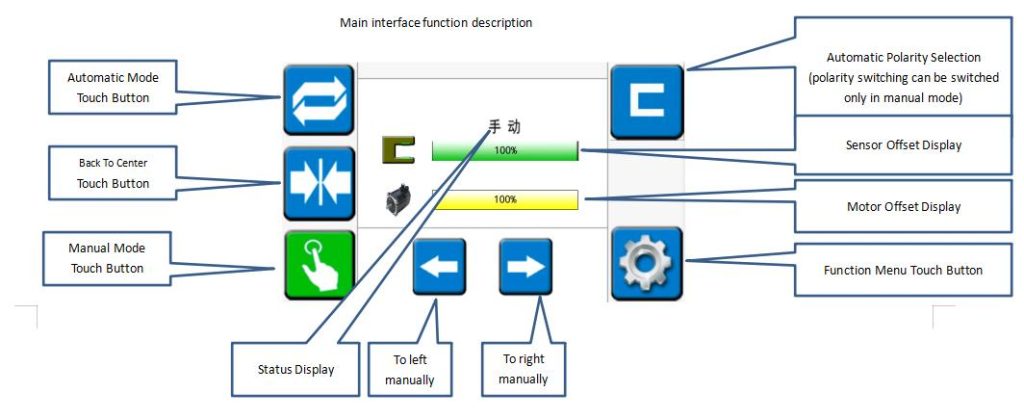
Infrared sensor calibration
For some materials that are not easy to identify, the infrared sensor is required to achieve the best web guide effect.
Steps
1. Long press the “SET” button to make the sensor light flash (release the button after flashing)
2. Tighten the material and put it into the position of the sensor near the light lens (the material will completely cover the circular light-transmitting sheet). Then wait for 3 seconds and remove all the materials from the sensor
3.Press the “SET” button until the light does not flash, and then release the button. The process of the calibration has been completed.

Common Problems In The Operation of The Web Guide System
1. The machine will swing to the limit alarm when it is switched to the “automatic” mode. (Confirm whether the correct polarity is correct and whether the sensor has a signal)
2. The speeds of the left and right swing are inconsistent in the “automatic” mode. (Check if the infrared sensor changes range from 0-100%)
3. When there are different materials in the “automatic” mode and the integrated machine does not swing, the infrared sensor is needed to calibrate the material.
Daily Maintenance and Operation Precautions
Before the web guide system work
1. Check carefully whether the power switch and the indicator light of the web control system are normal.
2. Check whether the electric indicator light is normal and the sensitivity of the electric eye and the motor.
3. Whether the magnetic powder brake can be braked in time.
4. Fill the gear contact position with lubricating oil to maintain the lubrication between the wheels and reduce mechanical wear to ensure the precision of the web guide.
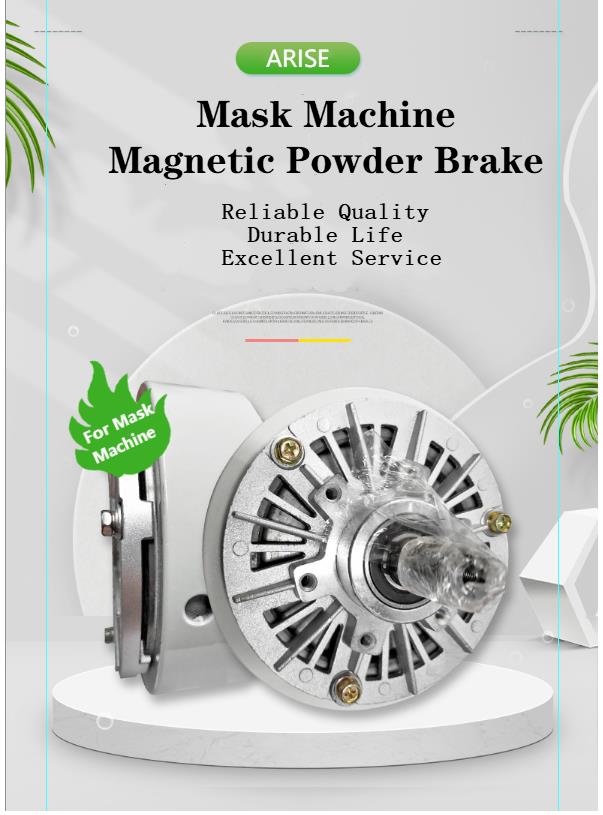
During the work of the web guide system
1. Is there any abnormality in the coordination of the electric eye, the control system, and the motor?
2.Listen to the sound, whether there is noise or excessive noise in the mechanical part.
3.Whether the temperature of the motor is too high.
After the work of the web guide machine
1. Turn off all power sources to prevent the rectifier from being on standby at any time.
2. Close the protective cover of the web guide control device to avoid objects hitting the device or damaging the control panel.
3. Protect the electric eye from damage by external objects.
4. Lubricate the motor bearings and screw rods.
5. Add lubricant to gears and magnetic powder brakes.
Test of The Web Guide System
After the web guide system has been installed on the machine, about the installation, please visit the article on how to install the web guide system
1. let the machine run first, if there is a deviation, adjust the upper layer of fabric firstly. For example, if it is to the left, it needs to be adjusted to the right. In the same way, if it turns to the right, you must adjust to the left.
2. Before turning on the web guiding machine, make sure that the fabric is aligned.
3. Then turn on the web guide equipment. After identifying the fabric, the probe is aligned with the red dot and the upper line is aligned with the edge. Then tighten the lower screw and the position will be located.
4.After locating the position, press the button of “automatic” mode. If there is an offset, it will all be aligned with the upper line.
5. Each layer is the same, and this layer should also be aligned with the red dot. The lower screw must be loosened firstly, and then the probe can be moved and aligned with the red dot.
6. After aligning the red dot and twist the black screw.
7. Then touch the “automatic” mode. If there is a deviation, the machine will swing and automatically correct it.
8. All the systems keep the “automatic” mode. Now the web guide runs automatically, and the machine will not run off when it starts.
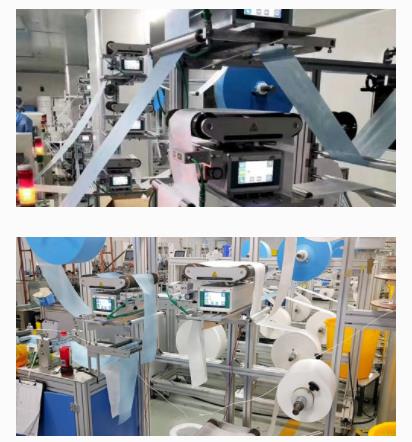
Arise web guide system can be widely used in various production processes of steel, corrugated paper, non-woven fabric, textile, printing, labeling, plastic film, building materials,etc. The guiding system can ensure continuous, precise control of the edges of the coil materials and limit the waste to a minimum。