A Comparative Analysis of the Different Types of Web Guiding Systems
Web guiding systems have transformed the manufacturing industry that relies on continuous web materials by enabling accurate alignment and tension management. As production demands increase, selecting the best web guide system becomes increasingly important. This article gives a thorough comparison of the various types of web guiding systems available, emphasizing their working principles, benefits, and ideal applications.
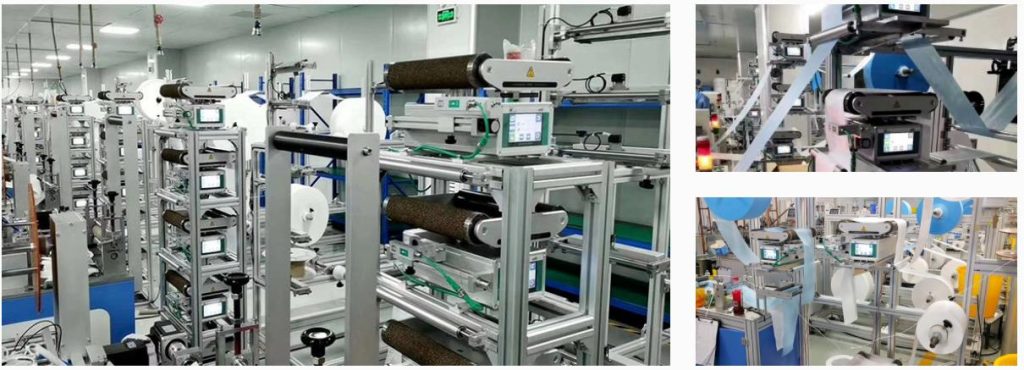
Line Edge Sensor-Based Web Guiding Systems
Line edge sensors, which are at the heart of these web guide systems, detect changes in light, infrared, or sound patterns as web materials pass over their field of view. These sensors receive signals that show the web’s alignment condition by emitting a beam of light, infrared radiation, or ultrasonic waves across the web. When the web is on its intended course, a continuous and constant signal is received by the sensor.
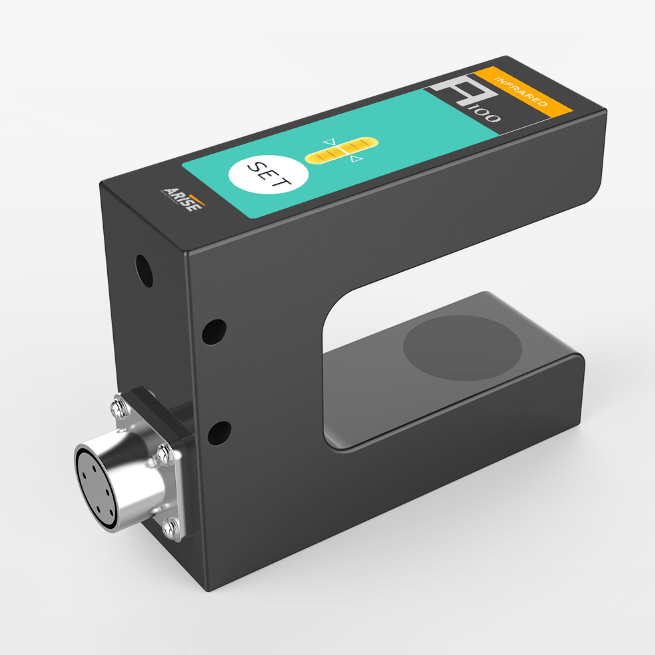
Working Principle
The fundamental value of line edge web guide sensors rests in their ability to detect misalignment quickly. Any variation from the planned alignment causes the received signal pattern to shift. This shift causes the web guiding system to make precise adjustments, correcting the web’s lateral position and returning it to the centerline or ideal alignment. Throughout the production process, this real-time feedback loop guarantees that the web materials remain exactly aligned.
Benefits
Real-Time Alignment: Line edge sensors give fast input, allowing for quick modifications and reducing misalignment.
Non-Contact Detection: These sensors provide non-contact sensing, which protects fragile materials.
Versatility: Line edge sensors can work with a wide range of materials, making them useful in a variety of sectors.
Ideal Applications
Printing: Ensuring precise alignment of paper or labels during printing processes.
Packaging: Accurately aligning packaging materials for consistent packing quality.
Textiles: Maintaining fabric alignment for flawless weaving or printing.
Labeling: Accurate label alignment on items or packaging materials.
Converting: In manufacturing operations, ensuring accurate cutting, slitting, and perforation.
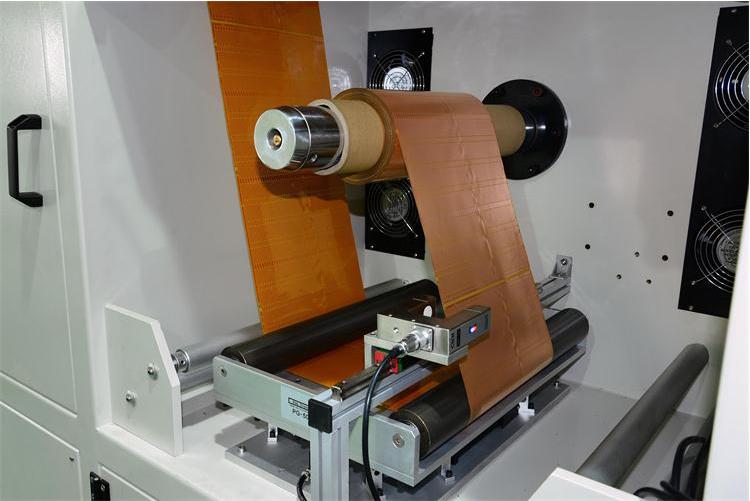
Tension Sensor-Based Web Guiding Systems
Tension sensors, which are responsible for monitoring and managing the tension forces given to moving web materials, are at the heart of web guiding systems. These sensors detect changes in tension and provide real-time input, allowing for fast adjustments to maintain optimal tension.
Working Principle
Load cells, dancer rolls, and ultrasonic, and magnetic sensors are all examples of tension sensors. The sensor detects variations in force as the web material is strained. The data collected is transmitted to a control system, which analyzes the information and initiates adjustments to maintain consistent tension across the web.
Benefits
Uniform Tension: Tension sensor-based devices maintain uniform tension across the web material, preventing flaws such as creases and stretching.
Versatility: Different sensor types are tailored to different material kinds and industrial processes.
Real-Time Feedback: Immediate changes ensure proper tension, which improves product quality.
Keeping a consistent tension for flawless cloth weaving.
Ideal Applications
Textile Weaving: Maintaining uniform tension for seamless fabric weaving.
Paper Manufacturing: Extrusion and lamination of plastic films require precise tension control.
Film Production: Precise tension control for plastic film extrusion and laminating.
Labeling and Packaging: Tension control during label application and packing material production.
Capacitive Sensor-Based Web Guiding Systems
The technique of sensing changes in capacitance induced by the presence of web material is at the heart of capacitive sensor-based web guiding systems. These sensors are particularly good in detecting the position and alignment of non-conductive or low-conductive materials, which can be difficult for other sensor types to detect.
Working Principle
Between the sensor and the web substance, capacitive sensors generate an electric field. The capacitance between them changes when the substance is present. The sensor detects this change and gives feedback to the control system. The control system analyzes this data and makes modifications to maintain optimal alignment.
Benefits
Alignment for Non-Conductive Materials: Capacitive sensors excel in aligning materials with low conductivity, which can be difficult for other sensor types to do.
Consistent Detection: Capacitive sensors provide reliable alignment detection regardless of material qualities.
Precision Alignment: These sensors provide high precision, which contributes to higher product quality.
Ideal Applications
Plastic Film Processing: Ensures precise alignment during plastic film extrusion and laminating.
Labeling and Packaging: Label alignment on non-conductive packing materials.
Paper Manufacturing: Accurate alignment of non-conductive paper during printing and processing.
Textile Production: Keeping non-conductive materials aligned during weaving and printing.
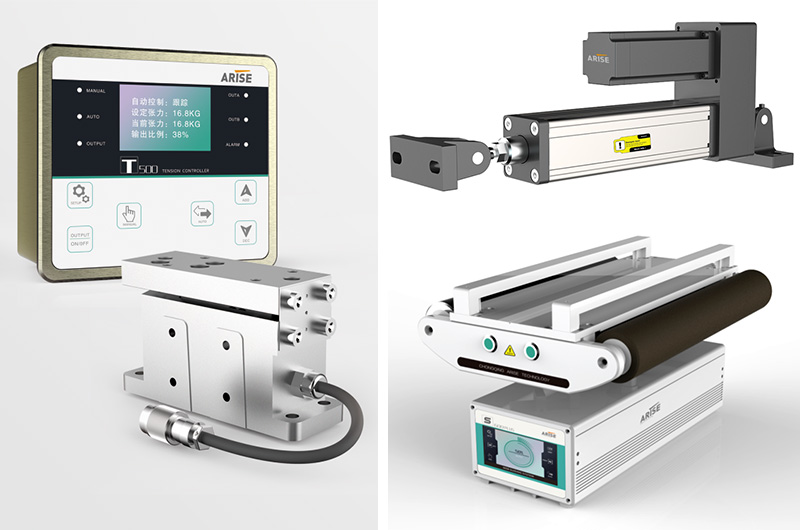
Summary
Understanding the complexities of each technology and its usefulness for various applications is critical in selecting the right web guiding system. Line edge sensor-based systems excel in quickly aligning different materials, whereas capacitive systems excel at non-conductive material alignment. Tension sensor-based web guide systems are critical for ensuring consistency, whereas laser sensor-based systems offer unparalleled precision.
When choosing web guide systems, manufacturers must consider aspects such as material qualities, production environment, necessary precision, and budget. Each system type has its own set of advantages and disadvantages, allowing manufacturers to tailor their selection to their own production requirements. In a world where precision and efficiency are essential, being able to select the correct web guiding system is a vital step in improving product quality, reducing waste, and maintaining a competitive edge in the dynamic landscape of modern manufacturing.