5 Key Points to Know What are Automatic Tension Controllers
Automatic tension controllers play a pivotal role in maintaining consistent tension throughout various production processes, ensuring quality, efficiency, and reduced waste. By automating tension control, manufacturers can overcome challenges such as material stretching, tearing, or misalignment, which can disrupt workflows and increase production costs.
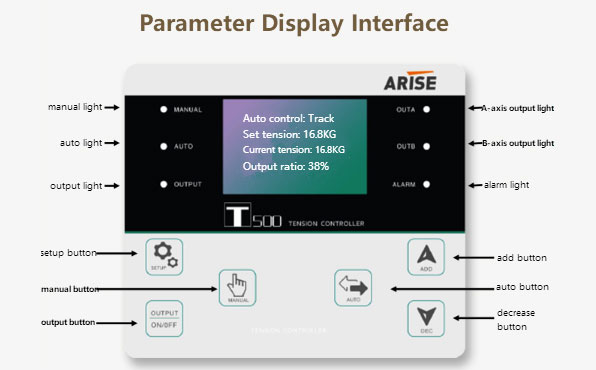
Table of Contents
The Significance of Automatic Tension Controllers
The primary function of an automatic tension controller is to monitor and regulate the tension of materials in real-time. These systems rely on sensors, such as load cells, dancer rollers, or ultrasonic devices, to measure the tension accurately. Based on these measurements, the controller adjusts the torque, speed, or braking force of the machinery to maintain the desired tension levels. This real-time adjustment is essential for processes where even slight variations can lead to defects or inefficiencies.
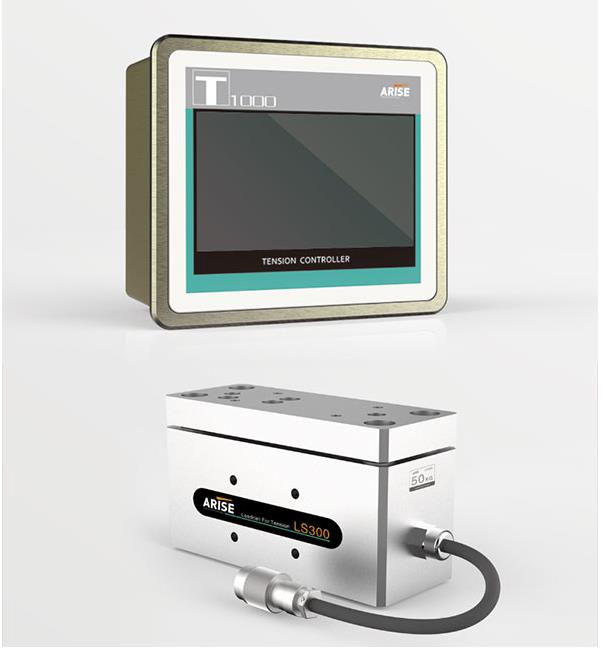
How Does An Automatic Tension Controller Work
An automatic tension controller works by maintaining consistent tension on materials as they move through industrial machinery. This is critical for processes like printing, packaging, textile manufacturing, and metal processing, where uneven tension can lead to defects, material damage, or production inefficiencies. The operation of an automatic tension controller involves sensing, adjusting, and controlling tension in real-time.
The process begins with tension measurement, which is typically done using sensors like load cells, dancer rollers, or ultrasonic sensors. Load cells measure the force exerted by the material on a roller or pulley, converting this force into an electrical signal. Dancer rollers, on the other hand, sense material slack or tightness by detecting the movement of a roller connected to the material. Ultrasonic sensors are often used to monitor roll diameter, especially in open-loop systems. The data collected by these sensors provides a real-time representation of the tension in the material.
Once the tension is measured, the controller processes the data and determines whether adjustments are needed. This is the role of the control unit, which interprets the signals from the sensors and compares them to the pre-set tension levels. If the actual tension deviates from the desired level, the controller sends signals to adjust the machinery, such as braking systems, motors, or clutches.
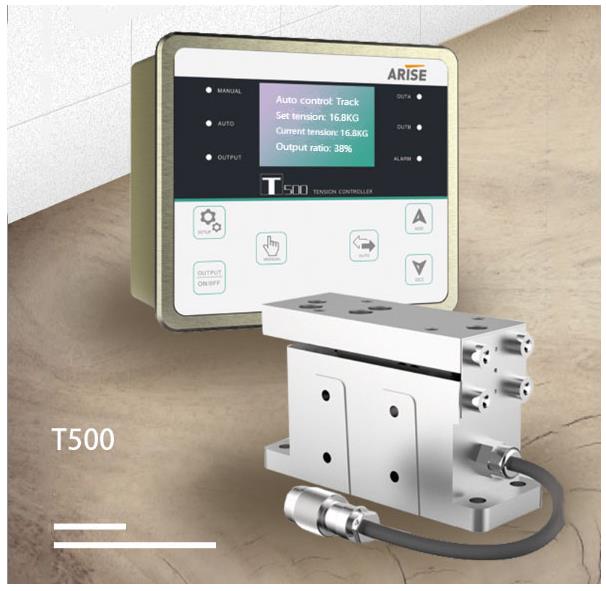
Types of Automatic Tension Controllers
Automatic tension controllers are categorized into different types based on their operational mechanisms and how they manage tension. Each type is tailored to specific industrial applications and requirements.
1. Open-Loop Tension Controllers
One common type is the open-loop tension controller, which relies on preset parameters rather than real-time feedback to regulate tension. These controllers are straightforward and cost-effective, making them ideal for applications where tension variations are minimal, such as processes with consistent material properties and uniform operating conditions. However, they may lack the precision required for more dynamic or high-speed operations.
2. Closed-Loop Tension Controllers
Closed-loop tension controllers are designed for applications demanding high precision. These systems use real-time feedback from sensors like load cells or dancer rollers to monitor tension and adjust accordingly. The continuous feedback loop ensures consistent tension, even when dealing with changing material properties or fluctuating operating speeds. This makes closed-loop systems well-suited for industries such as printing, converting, and textile manufacturing, where maintaining uniform tension is crucial for quality outputs.
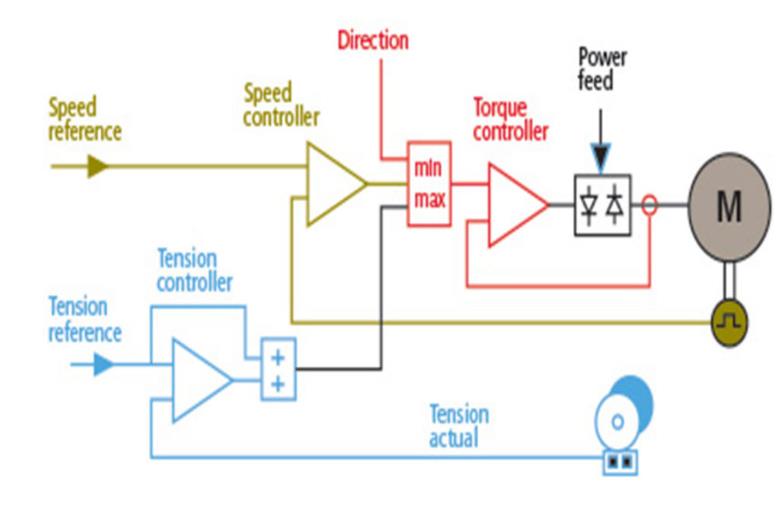
3. Hybrid Tension Controllers
Hybrid tension controllers combine the features of both open-loop and closed-loop designs, offering flexibility for production lines with varied demands. It can operate in open-loop mode during stable conditions and switch to closed-loop mode when higher accuracy is needed. Such controllers are particularly useful in multi-stage processes where the requirements may change at different stages.
4. Pneumatic Tension Controllers
Pneumatic tension controllers rely on air pressure to control brakes or clutches for tension adjustment. These systems are known for their simplicity and reliability, making them suitable for moderate-speed applications, such as paper and film processing. They provide smooth and rapid adjustments, ensuring consistent tension without requiring complex electronic systems.
5. Digital Tension Controllers
Digital web tension controllers are the most advanced option, leveraging modern electronics and digital interfaces. Equipped with programmable logic controllers (PLCs) and human-machine interfaces (HMIs), these controllers offer precise, programmable tension control. Many digital systems are IoT-enabled, allowing for remote monitoring and real-time adjustments. Their ability to integrate with Industry 4.0 frameworks makes them the preferred choice for modern industrial environments where automation and data-driven insights are essential.
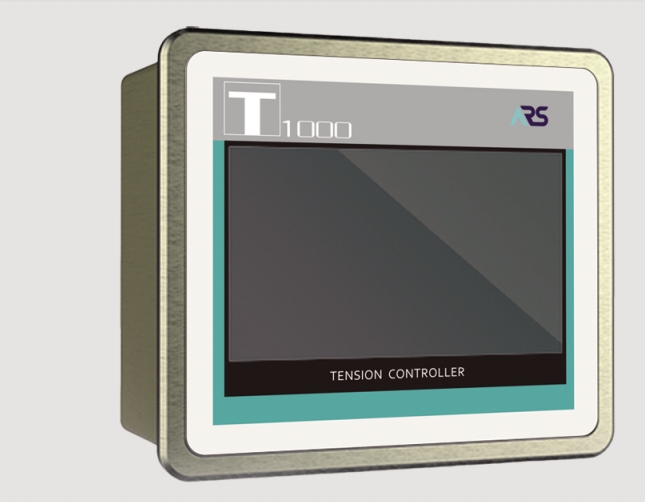
Applications of Automatic Tension Controllers
Industry | Application | Key Benefits |
Printing | Maintaining consistent tension during high-speed printing processes | Prevents misalignment, reduces waste, and ensures high-quality prints |
Textile | Controlling yarn tension in weaving, knitting, and dyeing processes | Improves fabric quality, prevents yarn breakage, and ensures uniform texture |
Packaging | Ensuring stable tension in film, paper, or foil during packaging operations | Enhances seal integrity, prevents wrinkles, and optimizes material usage |
Metal Processing | Managing tension in metal sheets or coils during cutting, slitting, and rolling | Prevents deformation, reduces material stress, and improves edge quality |
Paper Manufacturing | Regulating tension in paper rolls during unwinding, rewinding, and converting | Prevents tearing, ensures uniform winding, and reduces downtime |
Film and Foil Production | Ensuring precise tension for thin materials during extrusion, coating, and laminating processes | Prevents stretching, maintains uniform thickness, and ensures consistent quality |
Rubber and Tire | Controlling tension during rubber extrusion and tire cord processing | Ensures product durability, prevents material defects, and enhances production efficiency |
Wire and Cable | Maintaining tension during wire drawing, coating, and insulation processes | Ensures uniform diameter, prevents breakage, and improves coating consistency |
Flexible Electronics | Managing tension in conductive films and substrates during manufacturing | Ensures precise alignment, prevents material damage, and supports high-tech production needs |
Battery Manufacturing | Regulating tension in electrode films during assembly of lithium-ion batteries | Improves product reliability, ensures uniform layering, and enhances energy efficiency |
Future Trends in Automatic Tension Controllers
1. Integration of Artificial Intelligence (AI) and Machine Learning (ML)
One significant trend is the integration of artificial intelligence (AI) and machine learning (ML) into tension controllers. By leveraging AI, these systems can analyze historical data, predict potential tension issues, and adapt dynamically to changing operating conditions. Machine learning algorithms enable tension controllers to “learn” the behavior of materials and equipment over time, enhancing their ability to maintain consistent tension and reduce production downtime. This predictive capability is particularly valuable in high-speed and complex operations where manual adjustments may fall short.
2. IoT-enabled Tension Controllers
These systems connect to industrial networks, allowing real-time monitoring, remote adjustments, and data-driven decision-making. Operators can access tension control systems from anywhere, using dashboards that provide insights into performance metrics, maintenance needs, and potential faults. This connectivity aligns with the broader push toward Industry 4.0, enabling seamless integration with other automated systems and ensuring optimized production lines.
3. Energy-saving Technologies
Future auto tension controllers are likely to incorporate energy-saving technologies, such as regenerative braking systems, which recover and reuse energy during operation. This not only reduces operational costs but also supports sustainability goals, a growing priority for industries worldwide.
4. Multi-material Tension Controllers
With manufacturers increasingly working with diverse materials ranging from ultra-thin films to heavy-duty metals, tension controllers must adapt to varying material properties without compromising accuracy. Future systems will likely offer greater flexibility, with advanced sensors and algorithms that can seamlessly switch between different materials during production.
5. Advanced Sensor Technology
Advancements in tension sensor technology are also paving the way for more precise and responsive tension control. Next-generation sensors, such as laser-based systems or high-resolution strain gauges, provide more accurate tension measurements. Coupled with faster processing speeds, these sensors enable controllers to react in real time, even in highly dynamic environments.
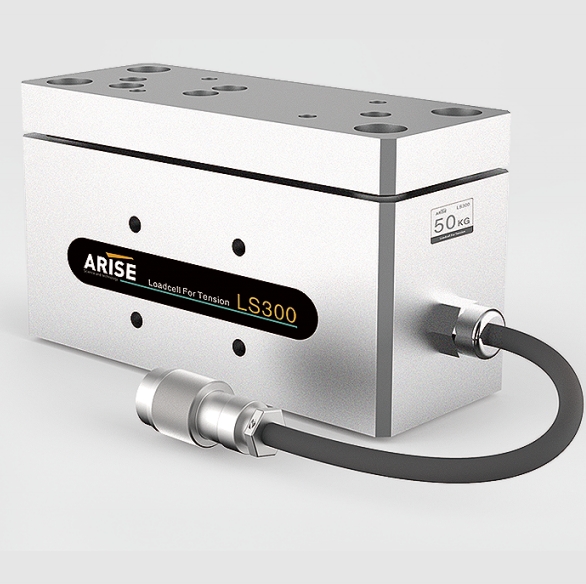
6. Compact and Modular Designs in Tension Controllers
Lastly, the trend towards reshaping tension controller hardware. Compact systems are easier to integrate into existing production lines, while modular designs allow for scalability and customization. As industries diversify, the demand for tailored tension control solutions will continue to grow, making modularity a critical feature.
Summary
Automatic tension controllers have become an essential component of modern industrial processes. Their ability to deliver precision, enhance efficiency, and reduce waste makes them invaluable for industries striving to achieve high-quality outputs in a competitive market. With advancements in digital technologies and smart systems, these controllers are set to play an even greater role in shaping the future of industrial automation.